Ford CEO Jim Farley emphasized the necessity of building out a supply chain in the US for critical battery minerals, calling it the constraint to accelerating EV production. Meanwhile, the American automaker continues manufacturing massive batteries, upwards of 140 kWh, for its full-size electric truck, the F-150 Lightning. Imagine how many EVs could be produced by making smaller, more efficient models. Perhaps like an electric Maverick?
Ford CEO claims battery supply is reason for constraints
Ford jumped out of the gate in 2022, selling 61,575 electric vehicles in the US and becoming the second largest EV maker domestically behind Tesla.
However, it also came at a price. Ford revealed last week it expects its EV business unit, Model e, to lose $3 billion this year after losing a combined $6 billion between 2021 to 2023.
Farley said in an interview with Yahoo Finance, “batteries are the constraint here,” as he went on to mention critical battery minerals like “both lithium and nickel are the key constraining commodities.”
The Inflation Reduction Act, passed last August, incentivizes sourcing and producing these minerals in North America or with the US’s free trade partners. However, as Farley goes on to explain:
We normally get those from all over the world — South America, Africa, Indonesia. We want to localize that in North America, not just the mining but the processing of the materials.
And perhaps more importantly, Farley adds that even raw materials mined in the US are often sent back to China for processing, which the US is trying to dissuade automakers from doing through grants and other incentives such as those in the IRA bill.
Although the actions have stemmed some domestic production capacity, China still accounts for over 70% of the market, with battery giants like CATL that continue gaining momentum (read more about CATL and Ford’s new LFP battery factory in the US).
Ford looks to take advantage of the new incentives with a plan to build its “largest, most advanced and efficient auto complex” in the automaker’s 118-year history.
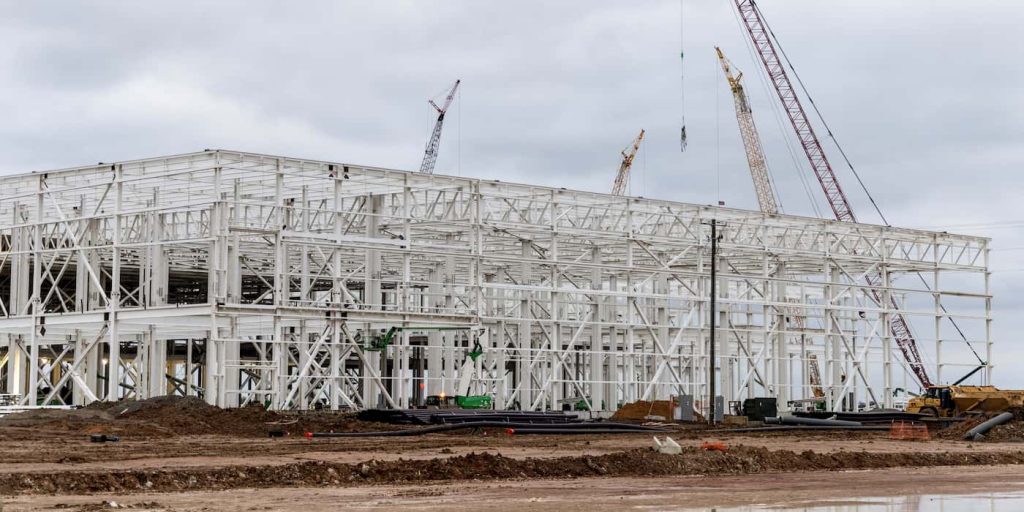
The initiative, called BlueOval City, includes three new battery plants in collaboration with SK Innovation and a new EV manufacturing complex where Ford will produce its second-generation electric truck and EV platform, codenamed Project T3.
Farley says the manufacturing process at the mega-campus will be a breakthrough with “radical simplicity, cost efficiency, and quality technology.”
Ford says the EV battery and manufacturing complex is on track to begin production in 2025. Altogether Ford expects to have 129 GWh of annual EV battery production capacity when the plants are fully operational.
Despite the ongoing battery constraints mentioned by Farley, Ford is aiming to produce 2 million EVs annually by late 2026.
Electrek’s Take
Ford is building out its domestic supply chain and manufacturing capabilities to streamline production, cut costs, and put the company in a position to succeed in the increasingly competitive EV market.
Meanwhile, Ford continues to crank out production of its massive F-150 Lightning with the extended range model battery size of 131 kWh. Perhaps, making smaller, more efficient EV models, something like an electric Maverick-sized truck could benefit the automaker even further.
Ford released its electric Explorer in the European market, a mid-size electric SUV based on Volkswagen’s MEB platform with an expected 52 kWh base battery with more powerful versions offering up to 77 kWh.
For every one Lightning produced, Ford could make two electric Explorers, almost three. Now, if Ford could do the same with a smaller, more efficient truck like the Maverick, production capabilities could easily double, if not triple.
Ford is looking at ways to overcome the battery constraints with new EV battery types like Iron phosphate (LFP) batteries, as well as advanced vehicle platforms and manufacturing processes, but it may be even more helpful to focus on making more efficient alternatives.
FTC: We use income earning auto affiliate links. More.